Polyethylene piping has become an increasingly popular choice for a wide range of applications thanks to its many advantageous properties. This versatile plastic material offers excellent durability, flexibility, chemical resistance, and cost-effectiveness that make it well-suited for various industrial and residential uses.
In this comprehensive guide, we'll take a closer look at what exactly polyethylene piping is, the different types available, its key benefits, common applications, and best practices for insulating polyethylene pipes.
What is Polyethylene?
Polyethylene is a thermoplastic polymer material made from ethylene gas. The long molecular chains that make up polyethylene can be produced in varying densities, resulting in different grades with unique physical and chemical properties.
The key characteristics that set polyethylene apart from other piping materials include:
-
Durability: Polyethylene is highly resistant to impact, abrasion, and stress cracking. This gives polyethylene pipes a long service life even when exposed to harsh conditions.
-
Flexibility: Polyethylene pipes can bend and flex easily to accommodate irregularities during installation. This flexibility also allows polyethylene pipes to withstand ground shifts and temperature fluctuations.
-
Chemical resistance: Polyethylene offers excellent chemical resistance and does not corrode when exposed to most acids, alkalis, salts, or solvents. This makes it suitable for carrying corrosive fluids.
-
Lightweight: Polyethylene is much lighter than traditional piping materials like steel, iron, or concrete. This makes polyethylene pipes easier to transport, handle, and install.
These properties make polyethylene an extremely versatile material suitable for a wide array of piping applications from gas supply lines to sewage drainage systems. Next, let's look at the different types of polyethylene pipes available.
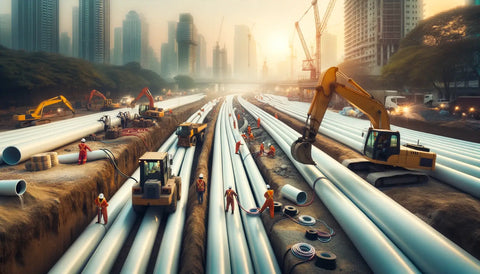
Types of Polyethylene Piping
There are two main categories of polyethylene piping – High-Density Polyethylene (HDPE) and Low-Density Polyethylene (LDPE). The density refers to the degree of branching in the molecular structure, which in turn affects the pipe's physical properties.
High-Density Polyethylene (HDPE)
HDPE has a simple molecular structure with less branching, giving it a higher density and increased strength. Key properties of HDPE include:
-
Higher tensile strength – HDPE pipes can withstand significantly higher pressures than LDPE.
-
Higher temperature rating – HDPE retains its integrity at temperatures up to 120°C.
-
Good chemical resistance – Impermeable to most solvents and non-oxidizing acids and bases.
-
Low coefficient of friction – Allows good flow characteristics, especially for gases and abrasive media.
With its high strength-to-density ratio, HDPE is well-suited for large pressure pipelines such as municipal water supply systems, gas pipelines, sewage drainage, etc. HDPE pipes are rated from PN6 to PN25 for different pressure requirements.
Low-Density Polyethylene (LDPE)
LDPE has a highly branched molecular structure giving it more flexibility but lower strength compared to HDPE. Key properties of LDPE include:
-
Flexibility – Easier to bend and install around obstructions.
-
Impact resistance – The branched structure provides good impact absorption.
-
Stress crack resistance – Not prone to cracking under prolonged stress.
-
Chemical resistance – Resists acids, bases, salts, alcohols, oils etc.
The flexibility and toughness of LDPE make it suitable for piping where frequent movement or impact is expected such as buried water service pipes and tubing for instrumentation and equipment connections.
So in summary, for high pressure applications choose HDPE, while for low pressure pipe insulation that requires flexibility, LDPE is more suitable. With those basics covered, let's now delve into the many benefits polyethylene pipe lagging systems offer.

Benefits of Polyethylene Piping
There are several key advantages that make polyethylene such an attractive and commonly used piping material:
1. Durability
Polyethylene lagging has an exceptionally long service life thanks to their high resistance to impact, weathering, abrasion and chemicals.
-
Impact resistance – The toughness and flexibility of polyethylene enables it to withstand physical impacts and ground movements that could easily fracture rigid pipes.
-
Corrosion resistance – Polyethylene pipes will not corrode or rust when exposed to moisture and soil. Even saltwater exposure has minimal effect on polyethylene.
-
Weather resistance – Polyethylene retains its mechanical properties even after prolonged exposure to sunlight, rain, and other weather elements.
-
Abrasion resistance – The smooth surface of polyethylene pipes minimize buildup and resist abrasive wear, ensuring reliable long-term performance.
With proper installation, polyethylene piping can easily last 50 years or longer without any degradation or need for replacement. This durability results in low lifetime costs.
2. Leak-tight Joints
Polyethylene pipelines can be joined into continuous lengths using heat fusion which melts the ends of pipes together. This creates a joint stronger than the pipe itself.
Additional benefits of heat fused joints include:
-
No leaks or seepage – The monolithic bonded joint eliminates leaks that can occur in threaded or gasketed joints.
-
Long lasting – When properly fused, the joint will last the full lifespan of the system with no separations.
-
Corrosion resistant – Heat fused joints will not degrade over time like metal joints are prone to.
-
Faster installation – No need for adhesives or sealants. Joints can be made in a matter of minutes.
The leak-free, seamless connections of polyethylene piping reduce maintenance costs and prevent groundwater contamination.
3. Flexibility
Polyethylene, especially LDPE, is a highly flexible plastic capable of elongating under stress. This offers several advantages:
-
Easy installation – Polyethylene pipes can bend around obstacles and fitted easily into trenches. There is no need for specialized fittings.
-
Expansion and contraction – The flexible pipes can expand and contract with temperature changes without compromising pipe integrity.
-
Withstand ground movements – The pipes can withstand bending and deforming due to minor ground shifts and seismic activity without breaking.
-
Impact resistance – Flexibility allows polyethylene pipes to absorb impacts, vibrations, and mechanical stresses that would seriously damage rigid piping.
The flexibility saves costs by reducing the complexity of installing polyethylene piping systems.
4. Lightweight
Polyethylene is much lighter than traditional metal and concrete piping materials. The typical weight of polyethylene pipes is at least 50% less than equivalent steel or iron pipes.
Advantages of the lightweight include:
-
Lower transportation costs – More polyethylene piping can be transported per load resulting in fewer trucks needed.
-
Easier handling – Lightweight pipes can be offloaded and positioned manually without heavy lifting equipment.
-
Simpler installation – Less need for specialized equipment or expertise to install lightweight polyethylene pipes. Digging, placement and backfill can be done quickly.
-
Lower buried cost – Does not require as much structural support to prevent sagging or floatation in buried applications.
By minimizing transportation and installation costs, the lightweight nature of polyethylene piping systems makes them more economical overall.
5. Chemical Resistance
Polyethylene offers excellent chemical resistance and will not degrade or corrode when exposed to most acids, bases, salts, fuels, solvents, and gases.
-
Acid resistance – Impervious to weak acids like formic and acetic acids as well as dilute mineral acids. Only oxidizing acids attack polyethylene.
-
Alkali resistance – Resistant to alkalis like caustic soda and potash solutions, milk of lime, etc.
-
Salt solution resistance – High resistance to salt solutions makes it suitable for marine applications and salt water conveyance.
-
Fuel and oil resistance – Hydrocarbon solutions have minimal impact on polyethylene pipe integrity.
-
Organic solvent resistance – Most solvents like alcohols, acetone, etc have no effect unless at very high concentrations.
This broad chemical resistance allows polyethylene to be used for a wide variety of corrosive chemical transportation applications.
6. Cost Effectiveness
When total lifetime costs are evaluated, polyethylene piping systems are often the most cost-effective choice compared to metal, concrete or plastic alternatives.
Factors contributing to the cost-effectiveness of polyethylene include:
-
Low material cost – Polyethylene resin is relatively inexpensive compared to metals and exotic plastics.
-
Lightweight and easy handling – Faster installation with less heavy equipment reduces labor costs.
-
Minimal maintenance – Excellent chemical and impact resistance prevents leaks or failures that require repair.
-
Long service life – Durable polyethylene pipes will last for decades without replacement.
-
Good flow characteristics – Low friction and smooth surface minimizes pumping/compression costs.
While polyethylene may have a higher upfront cost than some materials, the total cost savings over decades of maintenance-free operation make it worthwhile for many applications.
With those key benefits covered, let's now look at some of the most common applications that leverage the versatile properties of polyethylene piping.
Applications of Polyethylene Piping
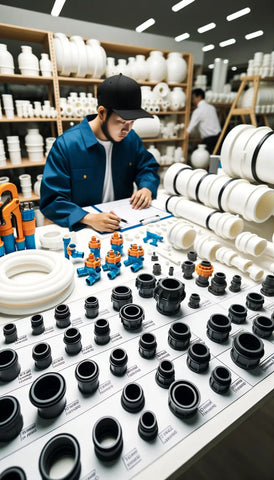
Thanks to its exceptional durability, tight jointing, flexibility, and chemical resistance, polyethylene is used extensively worldwide for the following applications:
Potable Water Supply
Polyethylene is an ideal material for drinking water supply lines. Properties that make it well-suited include:
-
No corrosion – Polyethylene will not contaminate water with rust, scale, or metal ions like iron pipes can.
-
Chemical inertness – Does not impart taste, odor, or color to the water.
-
Leakproof joints – Prevents infiltration of groundwater that could contaminate drinking water.
-
Withstands water hammer – Flexible pipes can handle hydraulic pressure surges without damage.
Polyethylene is approved for potable water contact by health and safety organizations worldwide. It poses absolutely no health risks.
Natural Gas Distribution
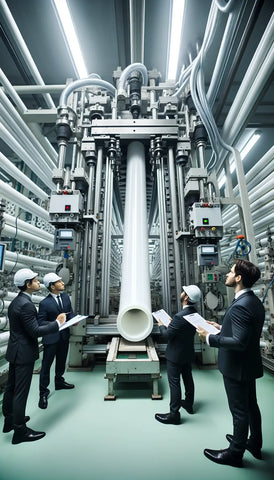
For natural gas utility supply lines, polyethylene is the preferred piping material due to:
-
Handling safety – Polyethylene is inert and will not combust or explode even with a gas leak.
-
Minimal leakage – Polyethylene's fused joints eliminate leaks that occur in threaded metal joints.
-
Corrosion resistance – Provides long service life in underground gas service lines.
-
Flexibility – Pliable polyethylene pipes can shift and move with soil without breaking.
Polyethylene gas pipes are durable, safe, and meet stringent industry standards for leakage.
Sewage and Drainage Systems
Polyethylene piping is the material of choice for underground drainage and sewage conveyance, providing:
-
Chemical resistance – Unaffected by salt, alkalis and acids that corrode concrete drainage pipes.
-
Smooth water flow – Low friction and non-stick surface maintains flow capacity over long term use.
-
Leakproof joints – Prevents exfiltration of sewage water into the surrounding soil.
-
Noise reduction – Polyethylene absorbs vibrations and noises associated with high-velocity drainage flows.
Thanks to its impermeability and chemical inertness, polyethylene protects environmental water quality in drainage applications.
Irrigation and Plumbing
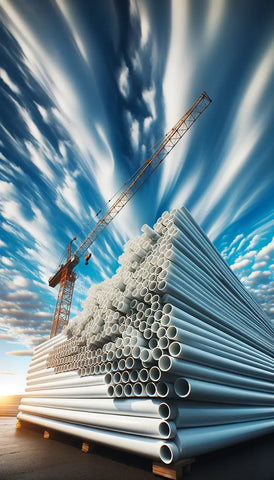
For irrigation piping and residential plumbing applications, LDPE is commonly used due to its flexibility:
-
Easy installation – Polyethylene pipes can snake around landscaping and contour to placement trenches.
-
Withstands abuse – Pliable pipes resist crushing and kinking from rocks and debris in buried lines.
-
Bendable connections – Polyethylene allows easy DIY connections without specialized tools or training.
-
Unaffected by sun exposure – Durable to extended UV exposure which degrades other flexible plastics.
Polyethylene's resilience and ease-of-use make it an ideal choice for both professional and DIY plumbing and irrigation projects.
Chemical Transportation
For safely conveying chemicals between storage tanks, reactors, and other process equipment, polyethylene excels due to:
-
Broad chemical resistance – Compatible with most common acids, bases, solvents, fuels, and gases.
-
Excellent temperature rating – Can withstand freezing temps to conveying superheated liquids.
-
Non-contaminating – Will not leach chemicals or substances into conveyed liquid.
-
Durable – Withstands vibration, thermal cycling, andexposure that degrades other plastics.
Polyethylene provides reliable long-term chemical transportation pipelines to minimize facility downtime and maintenance.
Geothermal Systems
In geothermal heating/cooling systems, polyethylene is the standard for ground loop piping because it:
-
Resists corrosion – Unaffected by soil acidity or moisture unlike metal pipe alternatives.
-
Flexible – Can snake through trenches easily and withstand ground shifting.
-
Heat fusion joints – Allow for leakproof connections essential below ground.
-
Good heat transfer – Conducts heat effectively into the circulating fluid.
Polyethylene's impermeability is essential for durable, maintenance-free geothermal ground loops.
This covers some of the most common applications, but polyethylene piping is also extensively used in landfill gas collection, methane drainage, mining, dredging, and industrial processed piping.
Now that we've covered polyethylene piping's benefits and applications, let's discuss how to properly insulate these systems.
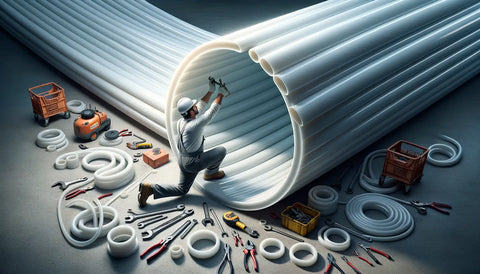
Insulating Polyethylene Pipes
While polyethylene piping is robust and durable, all piping systems require proper insulation to maximize performance, efficiency, and safety. The right insulation improves temperature control, prevents surface condensation, and provides personnel protection from hot/cold pipes.
Some key factors to consider when selecting insulation for polyethylene pipes include:
-
Temperature Range – Will the insulation need to withstand high temps up to 120°C or freezing conditions? Look for insulation rated for a wide temperature span.
-
Water Resistance – Since polyethylene pipes are often underground, the insulation should be waterproof and retain insulating value when wet.
-
Ease of Installation – Match the insulation flexibility to the layout to ensure it can be installed smoothly over bends and around valves.
-
Durability – Select long lasting insulation that won't degrade prematurely. Common choices include rubber, foam, and fibreglass.
-
Vapor Retardance – Prevent moisture contact and corrosion under insulation with vapor barrier films or wraps.
-
Heat Transfer – Minimize heat gain/loss and save energy with insulation that has optimal thermal conductivity.
-
Cost – Balance performance with budget considerations when selecting among insulation materials and thicknesses.
Some of the most common and effective insulation types for polyethylene pipes include:
Rubber Pipe Insulation
Rubber insulation like Armaflex provides excellent condensation control and thermal efficiency. Key properties include:
- Flexible, easy installation even on small diameter pipes.
- Closed-cell structure resists moisture.
- Available with self-sealing longitudinal joints for vapor tightness.
- Handles temperature extremes from -297°F to +220°F.
Fiberglass Pipe Insulation
Fiberglass insulation offers high temperature performance and fiber-reinforced strength. Benefits include:
- Excellent heat resistance up to 1000°F.
- High tensile strength resists crushing.
- Fibrous mat construction retards heat transfer.
- Available with all-service jacket suitable for outdoor use.
Foam Pipe Insulation
Foam insulations like polyethylene or polyolefin foam provide lightweight, cost-effective thermal protection. Advantages include:
- Lightweight, easy to handle and install.
- Closed-cell foam prevents moisture intrusion.
- Smooth exterior for easy cleaning.
- Designed for low to medium temperature applications.
- Low thermal conductivity reduces heat transfer.
Properly insulating polyethylene pipes improves energy efficiency, prevents condensation, minimizes heat loss/gain, and provides personnel safety from hot/cold surfaces. Consult insulation experts to select the right product for your specific piping temperature range, environment, and layout.
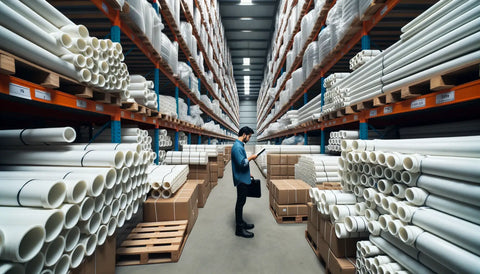
Conclusion
With its unmatched durability, leak-free jointing, chemical resistance, and cost-effectiveness, it's clear why polyethylene has become the go-to piping material for utility, industrial, commercial and residential applications worldwide.
Polyethylene piping offers reliable long-term performance whether carrying potable water, sewage, chemicals, gas or high-temperature fluids. By selecting the appropriate density and grade, polyethylene can be customized for pressures from low pressure drainage to high pressure gas transmission pipelines.
And thanks to its flexibility, light weight, and impermeability, polyethylene systems are easy to install, safe for underground applications, and offer low lifetime costs compared to alternative piping materials.
However, to maximize performance, polyethylene piping should always be properly insulated with materials like rubber, fiberglass or foam. Insulation reduces heat gain/loss, prevents moisture contact, and provides personnel safety.
So for your next plumbing, industrial, irrigation or utility project, consider polyethylene piping for a durable, low maintenance, and cost-effective piping solution. Paired with proper insulation, this versatile plastic material can handle even the most demanding piping challenges.